Engineering solutions in pediatric orthopedics
Dr. Robert Rizza, a professor in the mechanical engineering department, has spent his nearly 23 years at MSOE supporting the next generation of engineers and advancing research for pediatric orthopedics in Milwaukee in conjunction with the Medical College of Wisconsin and Children's Hospital.
Rizza’s research started in 2004 when he got a federal grant to use 3D printing to make orthotics for children with clubfoot. The orthotic helped patients who after casting and surgery still needed a solution to help with their pain. He went on to develop an orthotic through a federal grant to help with flatfoot before he moved into researching bracing for children with scoliosis.
The work to find an appropriate material for the back brace took many instances of trial and error. Through the help of Vince Anewenter at the Rapid Prototyping Center (RPC) on MSOE’s campus, Rizza was able to find out what materials were the newest on the market, try them out and see what would work the best as they designed and printed prototypes of the brace.
“As an engineer, you need to know what forces are being applied,” said Rizza. “How much should you push? How much should you pull? From there, you can use standard engineering principles and define what material, then how thick it needs to be.”
The brace has gone through many iterations and advancements over the years. Currently, Rizza has spent the past three years working on reducing the weight of the brace on the patient through finding a pattern structure that will make the brace more breathable and lighter. MSOE senior design students have helped over the years in his efforts. Seniors Kyle Norris, Preston Park and Agustin Rocha Bonilla are the latest group to assist with the project.
Through Selective Laser Sintering (SLS) 3D printing, the brace will now have an optimized octagonal lattice structure in the shell of the brace and engineered PEBA foam for an interior layer of comfort and airflow. This design will make it easier for patients to wear their braces for long periods of time with more comfort.
“Foam absorbs energy. If you don't absorb the right energy, then you don't provide enough cushioning. The beauty of the lattice structure is you put the lattice structure in the solid and the foam layer [of the brace] and you reduce the weight by 33 percent.”
The project involved extensive material testing, including compression and tensile analyses, to validate mechanical properties and develop design equations for the brace shell and foam. Students also helped with CAD and data analysis in Rizza’s own developed software.
Rizza is thankful for the work and support of senior design students—both past and present—the RPC, Sheku Kamara and Vince Anewenter for their assistance to this research over the years.
This project will be highlighted among many others at MSOE’s annual Senior Design Showcase held in May to celebrate the work of students in collaboration with outside organizations and academic departments at MSOE.
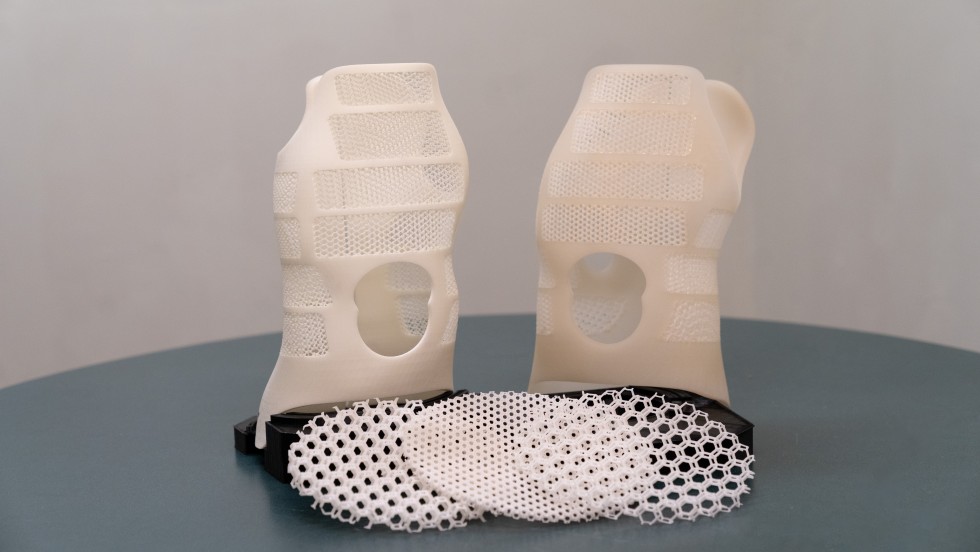
Prototypes of the back brace
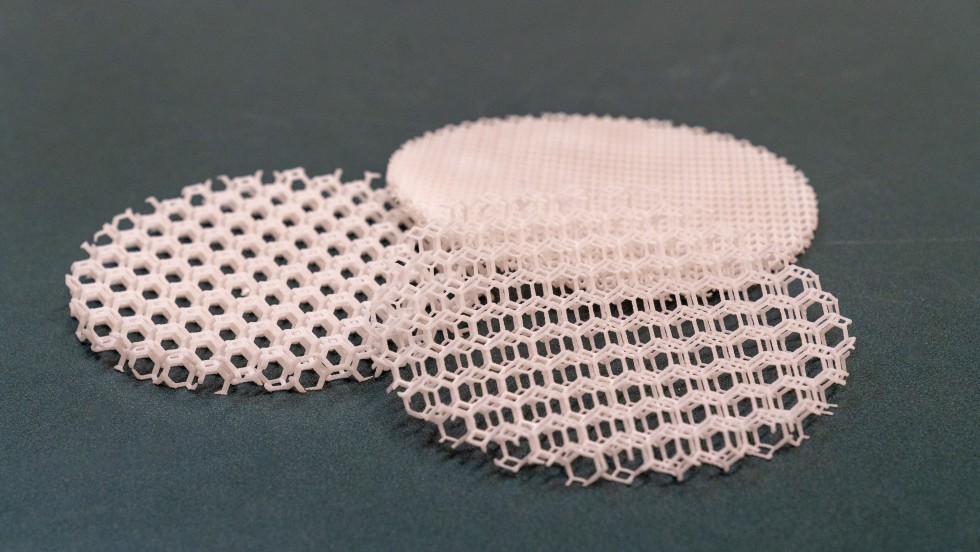
PEBA foam samples in various lattice patterns
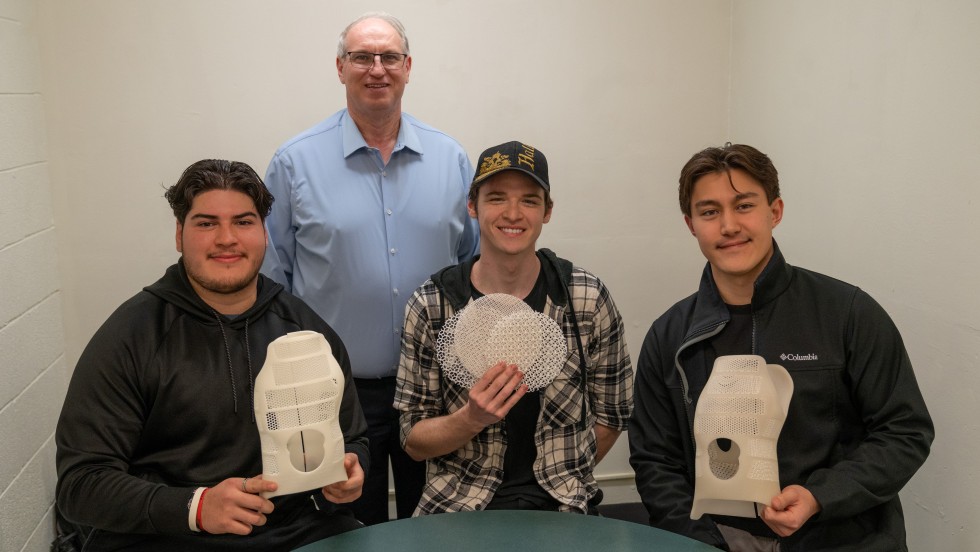
From left to right: Agustin Rocha Bonilla, Dr. Robert Rizza, Kyle Norris and Preston Park