ME students develop next-gen turbofan engine for wide-bodied aircraft
For their senior project, mechanical engineering majors Tazmar Dawkins, Charlie Gannon, Chris Imholte and Cadence Ruiz set out to improve fuel efficiency for a commercial wide-bodied aircraft. Their work followed an American Institute of Aeronautics and Astronautics (AIAA) Undergraduate Student Design Competition Request for Proposal (RFP).
The team presented their design of a next-generation ultra-high bypass ratio turbofan engine to power a commercial wide-bodied aircraft that cruises at subsonic speeds to other students and a panel of experts from industry and NASA. This happened in April at the AIAA Region III Student Conference hosted by the University of Akron in Ohio. The conference drew students from Wisconsin, Indiana, Illinois, New York, Boston, Kentucky, Ohio and Michigan.
“Since starting at MSOE and entering the mechanical engineering field I gained a huge liking of planes and how they operate,” said Gannon. “It has always fascinated me how such a large heavy machine could fly through the sky so easily. When we were presented with the options for our senior design I naturally gravitated to this project. I knew that it would give me more time to learn more about aircraft and flying as well as provide me with an excellent opportunity to interact with different experts in the aerospace field.”
Ultra-high bypass ratio turbofan engines are used in commercial wide-bodied aircraft because they deliver the necessary thrust to carry heavy payloads over long distances. They also consume less fuel and produce fewer emissions. Wide-bodied aircraft have two passenger aisles and can comfortably accommodate greater numbers of passengers and cargo.
Using GasTurb 14 to model the engine and perform various trade studies, the students completed a detailed validation study using data provided in the RFP for the current baseline engine. Their new design reduces thrust-specific fuel consumption by 8% and decreases engine mass by 5% while meeting the minimum takeoff thrust requirement of 193.06 kN and fitting inside the baseline engine nacelle (a streamlined container for aircraft parts such as engines, fuel or equipment). Since the entry date for this engine is 2035, a secondary goal of increasing the turbine inlet temperature by 5% through material advancements was included to further improve the cycle performance and reduce the engine weight. Finally, a full mission analysis was also performed to confirm that the total fuel burn during a typical flight was lower than that of the baseline engine.
One of the biggest takeaways from the AIAA conference for Gannon was realizing, “A certain task doesn’t have to be done one concrete way rather it can be done a variety of ways and still yield good results. I saw this through all the various projects that we watched being presented.”
This was a comforting realization for the team since they had faced challenges in their own work and had to adapt. For example, Gannon said, “The proposal we were originally given had a typo in it that suggested that the aircraft was flying at supersonic speeds. In reality that wasn’t possible, so this meant a lot of our analysis had to be reworked.”
Dr. Prabhakar Venkateswaran, associate professor and vice chairperson of the MSOE Mechanical Engineering Department, served as the team’s project advisor.
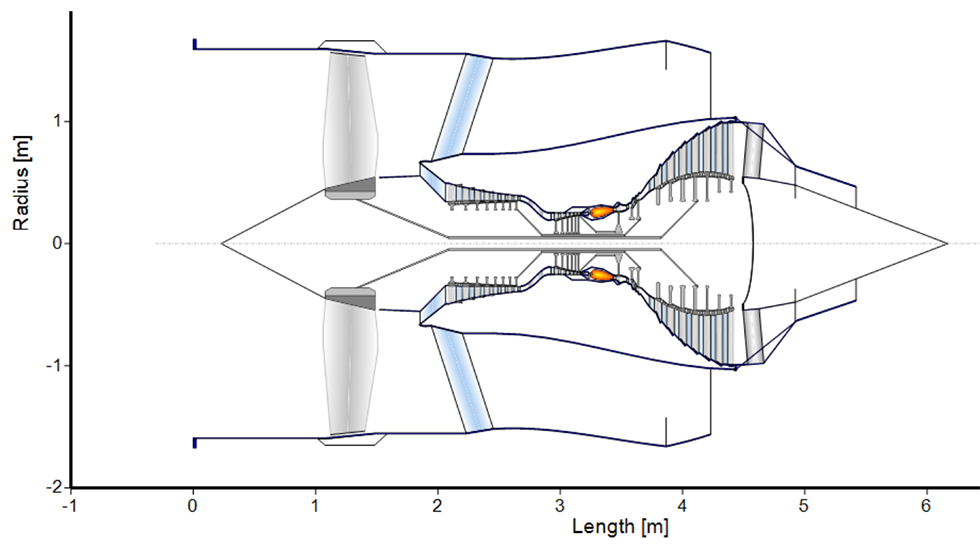
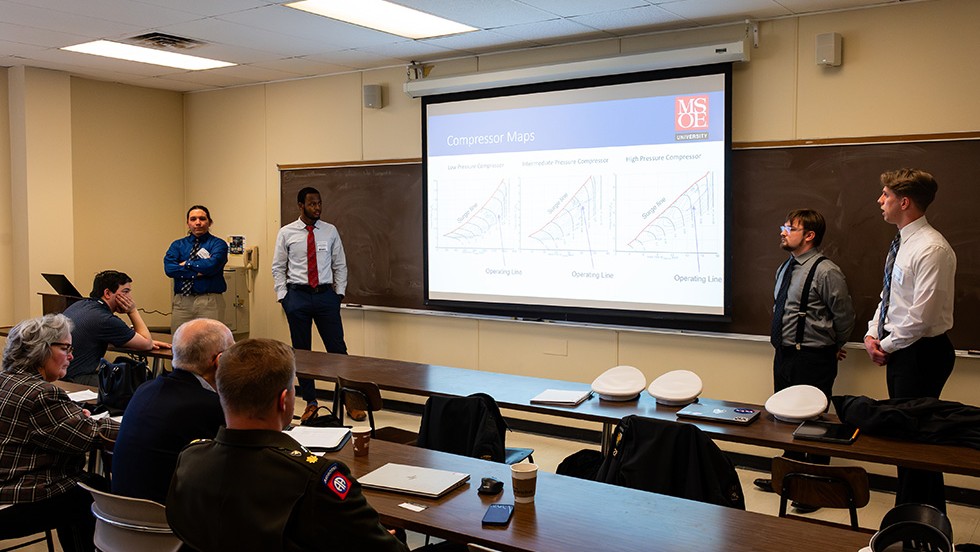
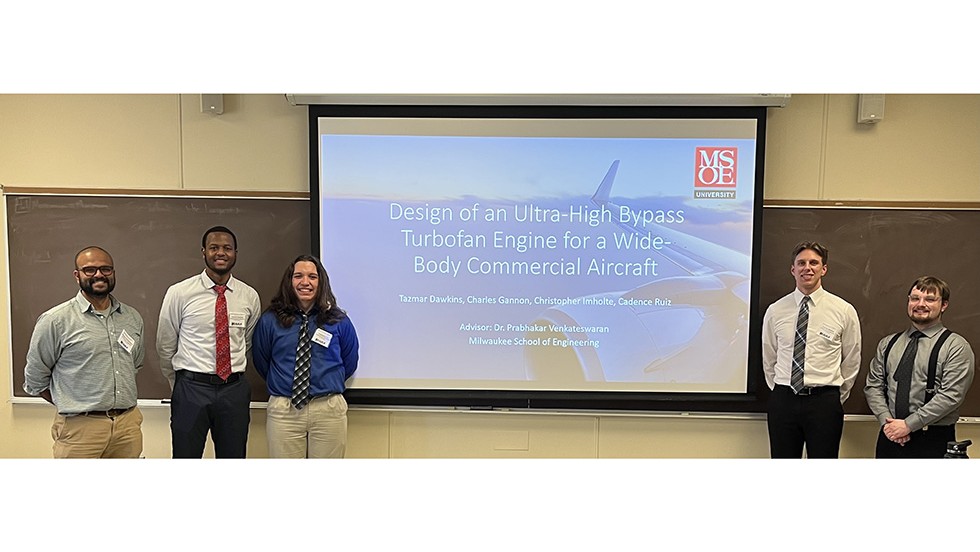
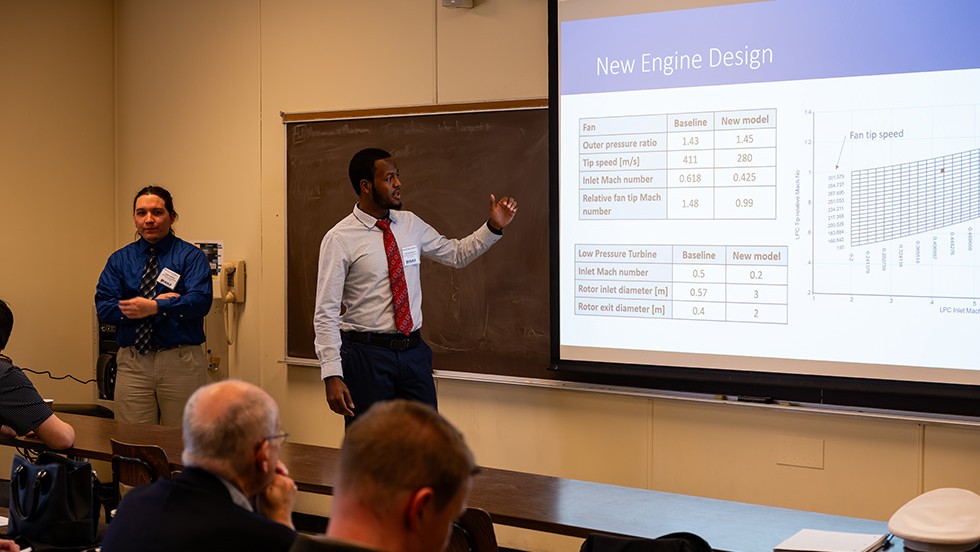